Rado et la céramique La beauté de l'industrie
Rado est une marque de montre dont nous avons chacun un souvenir plus ou moins clair et similaire. Celui de la fine montre des années 1980 habillée de noir, brillante et qu’un membre de la famille a toujours porté. Cette Rado Integral, pour la première fois réalisée en céramique et apparue en 1986, nous offre rapidement les clés de lecture d’une marque encore à mon sens trop discrète sur notre territoire.
Nous avons eu le plaisir de nous rendre là où l’histoire de Rado s’est écrite et s’écrit encore et de pénétrer les locaux de Comadur, entreprise du Swatch Group où le miracle, entre autres, de la céramique se produit.
D’entrée de jeu, nous avons le plaisir d’échanger avec Adrian Bosshard, CEO de Rado depuis le mois de juillet 2020. Comme de nombreux CEO de larges entreprises, il nous dévoile, en ouvrant les portes de son bureau, un pan « secret » de son histoire : celui de la moto. Une photo de lui à 4 mètres du sol en moto cross 500cm3, ou encore une compilation de bribes de compétition en moto de course sur Honda ou Yamaha. Une gentillesse et une ouverture d’esprit qui font aujourd’hui partie de Rado.
Ses premiers mots, à propos de Rado, se rapportent au fait que Rado est une marque pionnière et à la recherche constante de nouvelles façons de se démarquer en conservant son identité, aussi grâce à la force d’un groupe comme le Groupe Swatch. Rado imagine, dessine, se pose des questions mathématiques et métaphysiques, et Rado assemble, sans être une manufacture au sens premier du terme. À la fin en tous cas, après toute la réflexion préalable à de nouveaux produits, un boitier peut venir de chez Comadur, le mouvement de chez ETA, et les aiguilles de chez UNIVERSO, j’en oublie forcément.
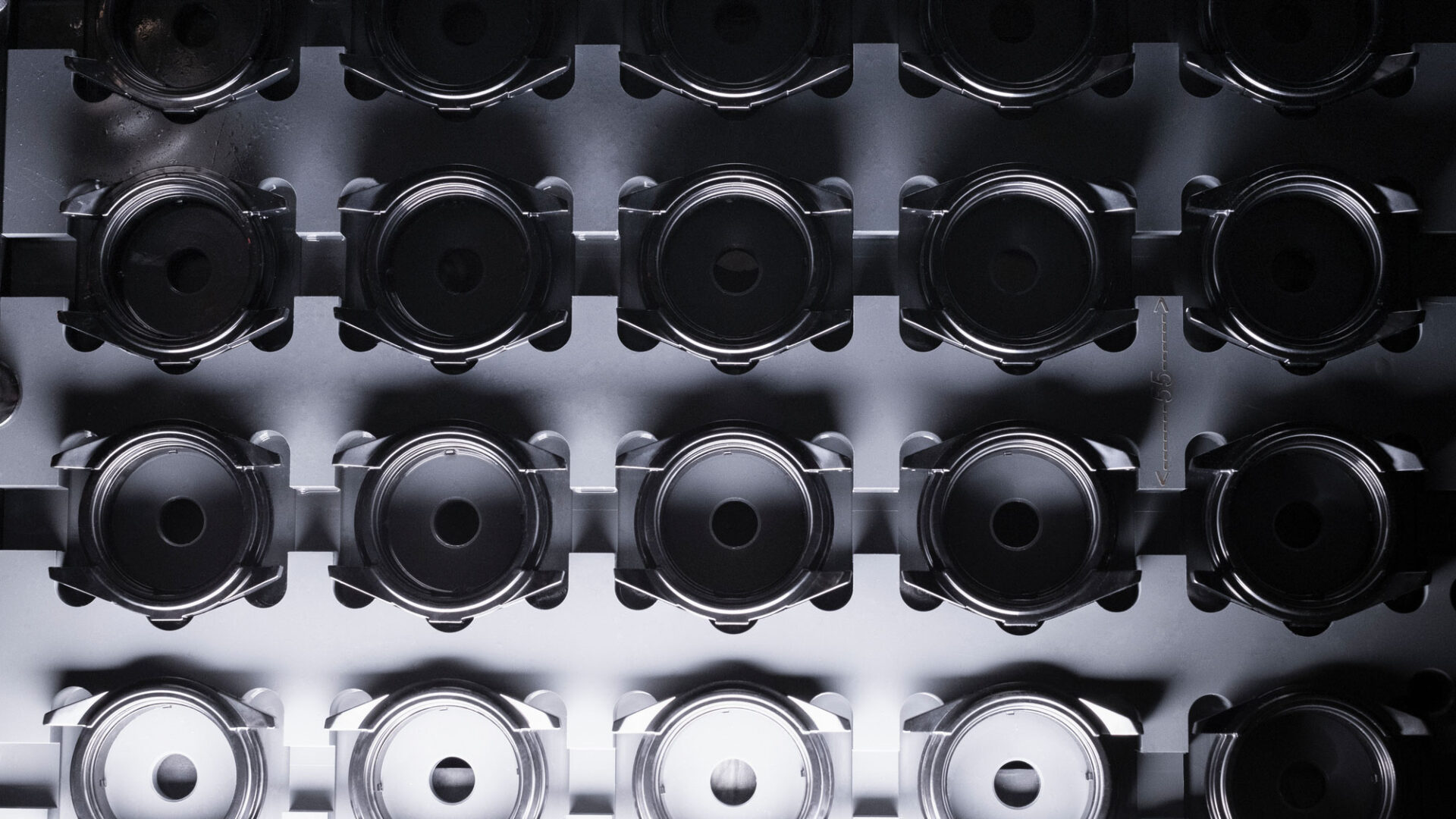
RADO
Au sein du Swatch Group, Rado fait partie des « jeunes » marques. Le mot « jeune » est à remettre dans le contexte d’autres marques du groupe Swatch jusqu’à bi-centenaires.
Les débuts de Rado se place sous le giron de l’entreprise Schlup & Co. Pas de montres en vue mais la production depuis sa création en 1917 de pièces diverses et variées, en particulier pour les mouvements. La marque Rado est déposée en 1928 avec comme horizon celui de produire des montres sous ce nom chez Schlup & Co d’ici à quelques années. C’est chose faite en 1957 avec la présentation de la collection Golden Horse. Probablement une référence à l’hippocampe, alors symbole de la collection pour montrer les efforts due la marque en matière d’étanchéité. Mais ce n’est pas vers quoi la marque se tourne tout de suite.
La célèbre DiaStar apparaît en 1962, et c’est une étape et un grand succès pour Rado. Pour la première fois, du métal dur est utilisé pour la confection du boitier. Le métal dur, ici sous forme de carbure de tungstène, est alors 5 fois plus dur que l’acier. Ajoutez-y un verre saphir taillé comme une pierre précieuse, et Rado est résolument en avance en 1962. D’ailleurs, quelques années plus tard avec l’Anatom, Rado introduira pour la première fois une montre avec son bracelet en métal dur.
Vous voyez où nous mène le métal dur ? À la céramique, indéniablement.
Il faudra attendre 1986 pour l’utilisation de la céramique sur la fameuse Integral aux formes très carrées et rectangulaires, et 1990 sur la Ceramica qui dévoilera cette fois le boitier et le bracelet réalisés intégralement en céramique noire. Le moment de l’apparition du noir en horlogerie et qui marquera Rado. Je vous passe quelques évolutions comme celles de la céramique blanche en 1991 et la céramique couleur acier en 1993, et nous ferons un pas en avant jusqu’en 2011 avec la présentation de la True Thinline, qui n’est autre que la plus fine montre réalisée en céramique haute technologie.
Ce que nous voyons donc au siège de Rado, à Lengnau, aujourd’hui, n’est autre que le contrôle de tout ce qui arrive pour être assemblé, avant d’être rigoureusement testé. Les têtes de montre une fois assemblée rejoignent une batterie de test, où la précision est mise à l’épreuve dans 5 positions, avant de passer aux tests d’étanchéité sous vide et sous pression, hormis pour les montres de plongées qui sont testées dans un autre laboratoire du Swatch Group et sous l’eau.
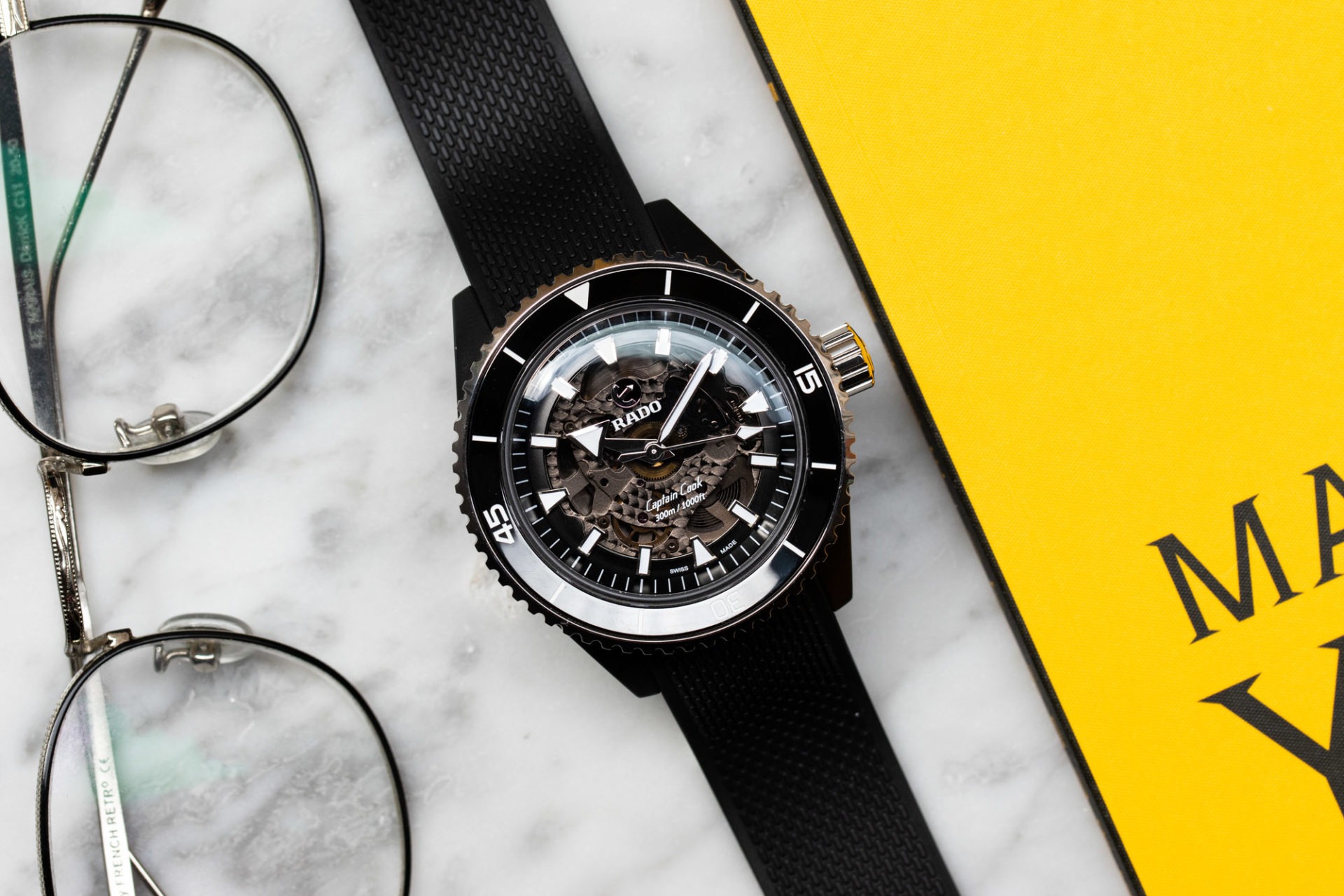
Il est amusant de comprendre où Rado excelle, géographiquement parlant. La marque ayant été pionnière au XXe siècle en Asie et au Moyen-Orient en y installant de nombreux centres de service et en ayant fait jouer du marketing en masse et assez rapidement. Sur ce genre de grandes affiches de rue, un peu partout. On comprend ainsi pourquoi l’Inde est parmi les trois premiers marchés pour Rado. L’Europe n’est pas sans restes, quand la Suisse évidemment, mais aussi l’Allemagne et l’Autriche font figure de bons élèves alors que l’Italie, la France et l’Espagne sont en potentiel.
Rado a donc fait figure de pionnier dans la céramique, avant d’en inspirer d’autre, tout en gardant aujourd’hui une longueur et une image d’avance. Notamment sur quelques procédés scientifiques dignes d’un projet de voyage vers une exoplanète.
comadur : la beauté de l’industrie
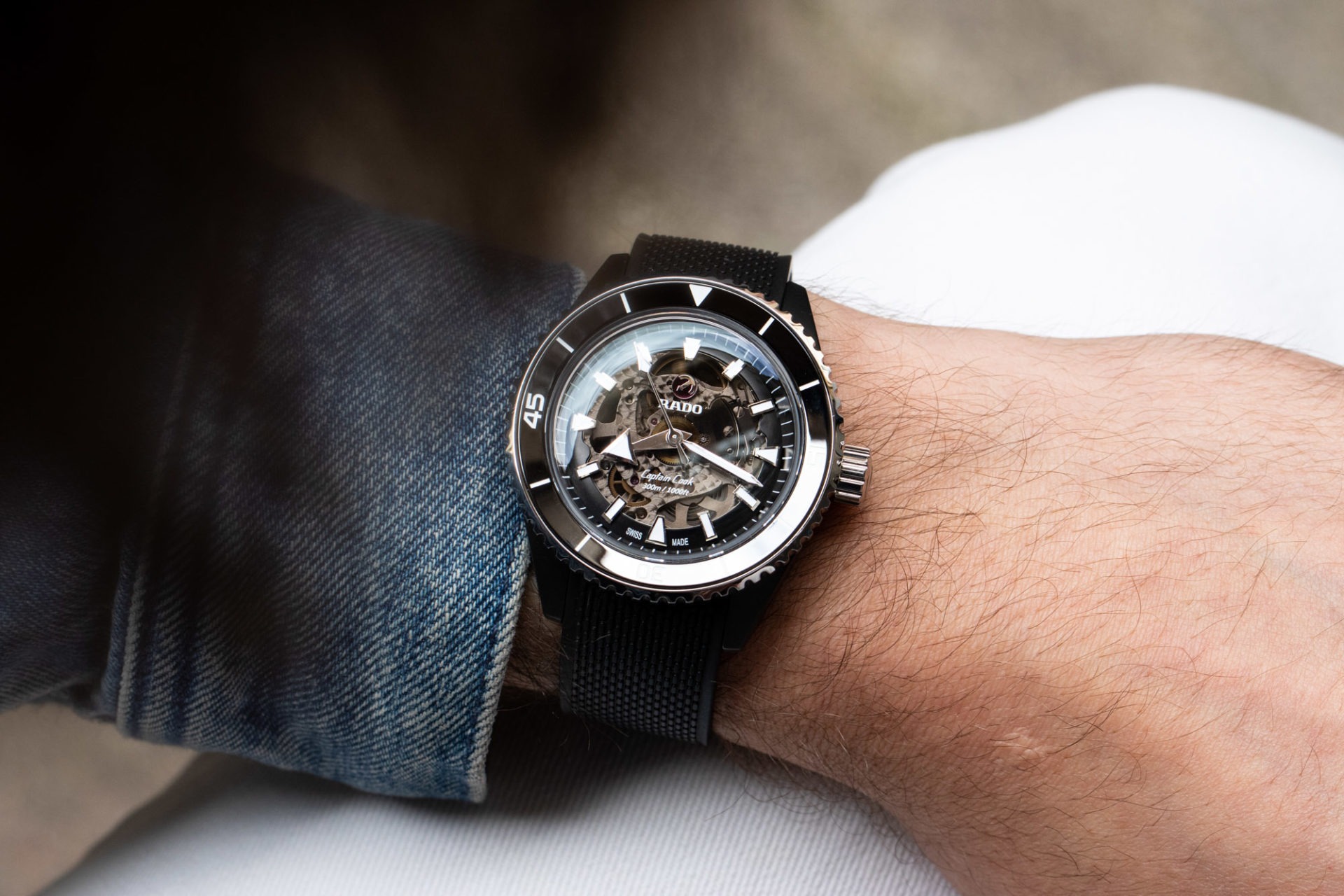
Comadur, société intégrée au Swatch Group, représente le laboratoire et l’industrie qui va servir à faire naitre des boitiers, des lunettes, inserts, bracelets et qui maitrise l’art du verre saphir et des micro-composants tels les rubis et autres micro-aimants. J’en oublie probablement.
Chez Comadur, pas de téléphone portable, pas de photos, on ne rigole pas avec la confidentialité. Après quelques rapides explications, nous entamons un tour des différents étages, où les personnes s’activent chacune bien à son poste, entre des machines protéiformes, parfois bruyantes, et où il sent bon l’huile et la machinerie lourde.
Sur une échelle de dureté, l’échelle de Vickers, la céramique se trouve à 1.250V quand l’acier est à 200 et le titane 300. Rado utilise, via les outils édentâmes Comadur, la technique d’injection pour la céramique. Tout commence par une petite pincée de poudre, de l’oxyde de zirconium. Cette poudre est ensuite transformée en unités plus grandes sous forme de granulés, par mélange avec des polymères qui servent d’aide à la mise en forme. Après avoir été débarrassés de toute forme d’impureté que l’on pourrait retrouver par la suite, une première forme est obtenue. Comment ? Par l’injection de ces granulés par 50 tonnes de pression dans des moules très particulier ayant déjà la forme du boitier, mais seulement chauffés à quelques centaines de degrés. Vous avez alors une forme de boitier d’assez grande taille entre les mains.
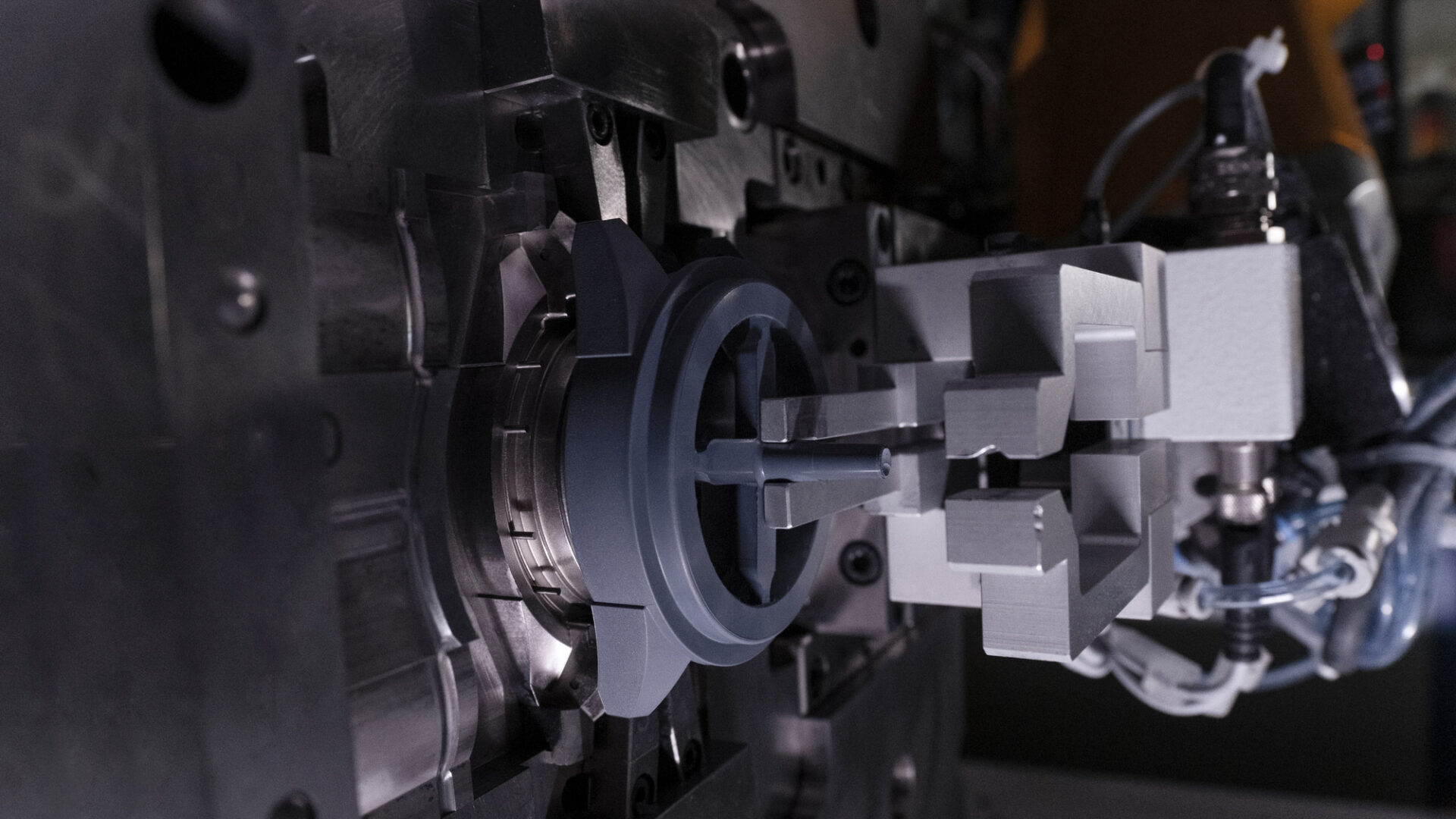
Vient ensuite le procédé de cuisson. Nous pénétrons alors une salle de fours, dont la température interne atteint les 1.400 degrés et où des piles rigoureusement ordonnées par couleurs n’attendent que de vivre l’enfer de chaleur. Cela permet de voir ce premier boitier réduire de 23% en taille, et ainsi prendre sa forme finale. Tout cela parait facile raconte ainsi, mais il faut prendre en compte la minutie des réglages de détails permettant de tomber exactement sur la bonne taille finale, et dans la même teinte de couleur, et ce après des milliers et milliers d’occurrences.
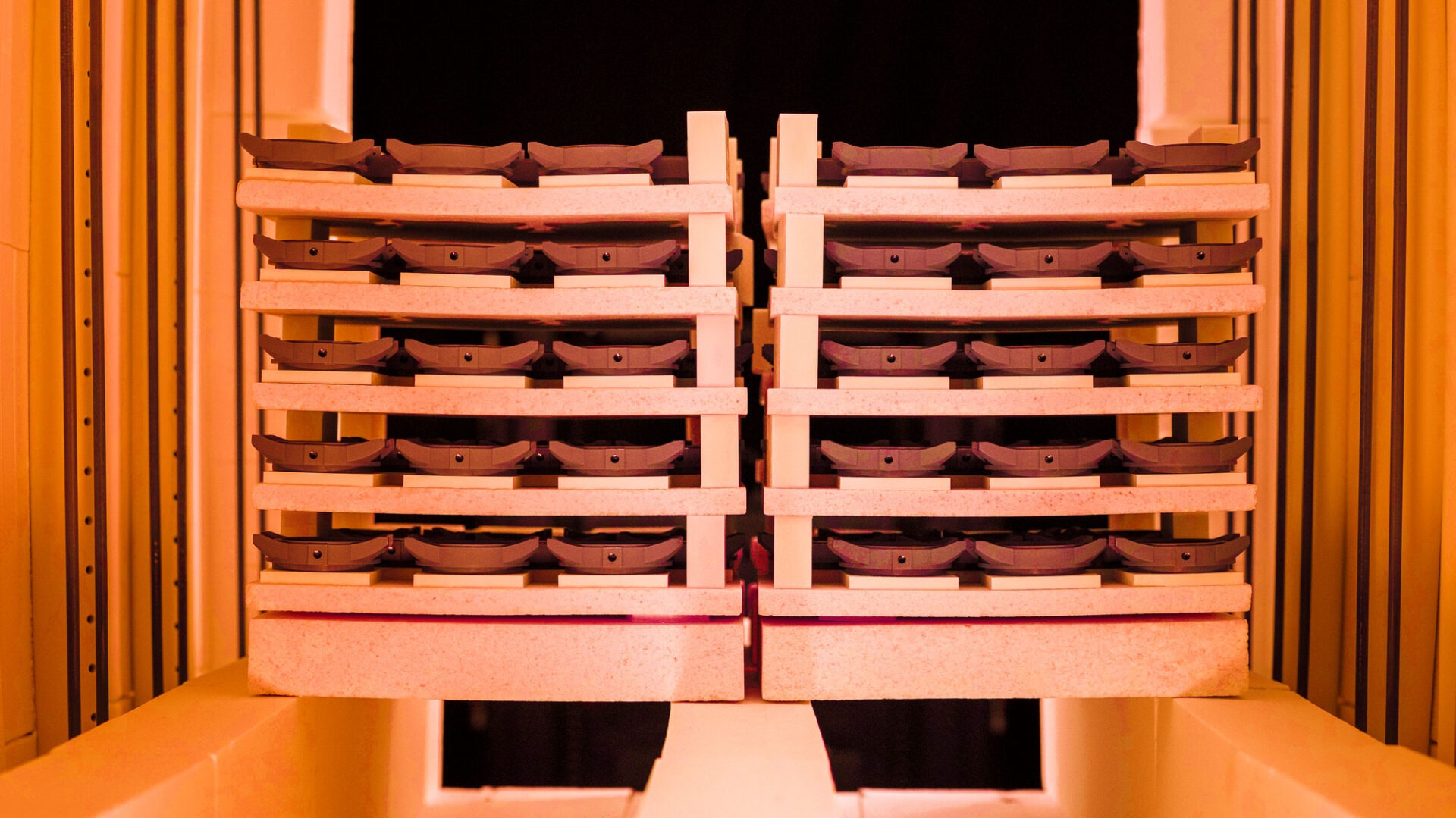
Vous pensiez que c’était fini ? Le boitier doit encore passer dans la « salle des tambours » comme j’aime à l’appeler, où dans de grands récipients sont mélangés les boitiers à de petits morceaux de céramique qui par les mouvements similaires à une machine à laver et pendant plusieurs heures vont polir le boitier. Évidemment, des finitions plus artisanales seront nécessaires pour obtenir des finitions parfaites, et toujours dans le même bâtiment.
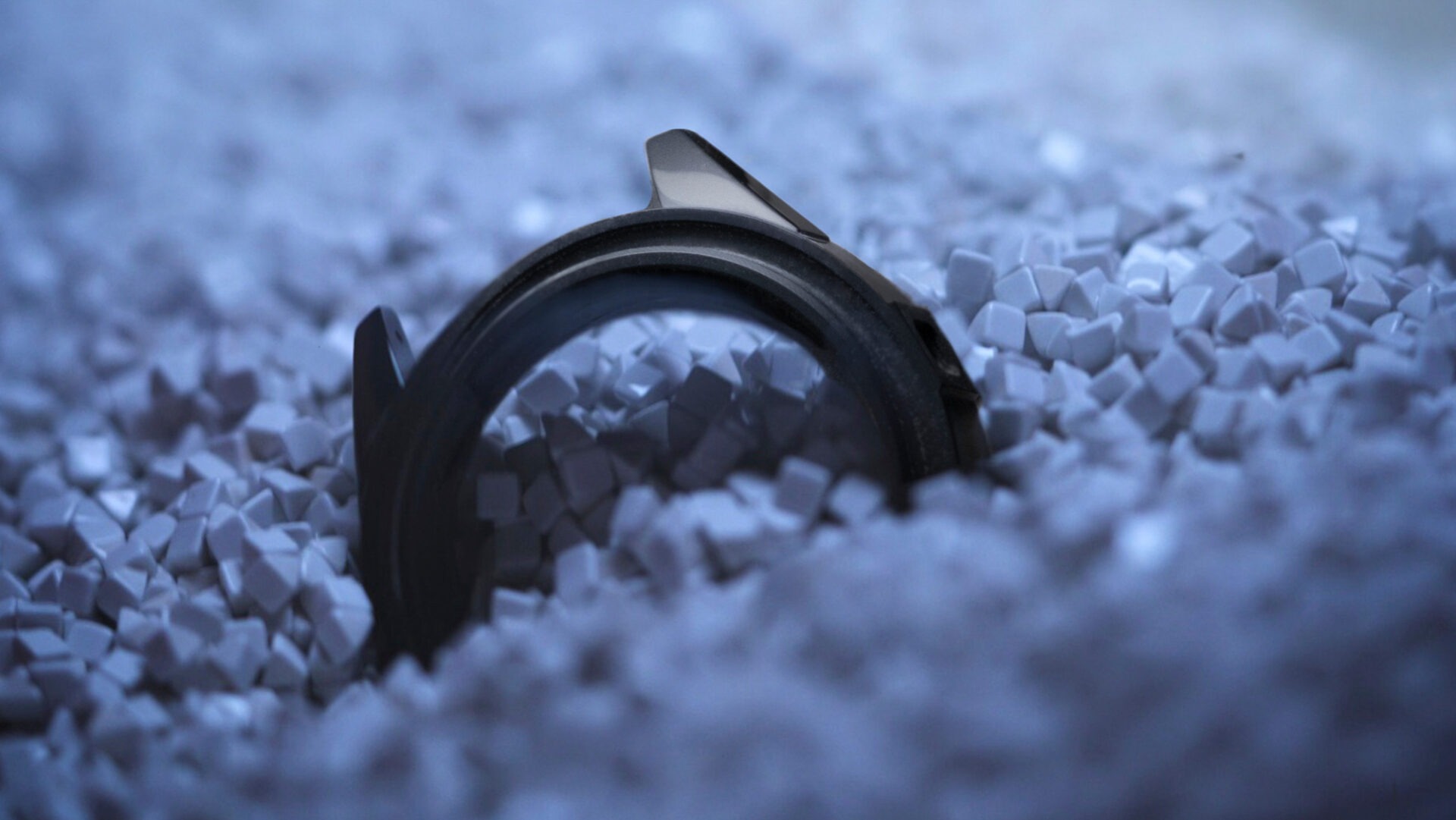
Le meilleur pour la fin. Si vous êtes amateurs d’astronomie et des scénarios possibles pour nous rendre dans un futur lointain sur une exoplanète, vous êtes alors familiers avec le concept de moteur à plasma. Durant cette visite, nous avons eu le plaisir de nous rendre dans une salle un peu particulière, où tournent deux fours à plasma. Trois gaz, hélium, méthane et argon, sont chauffés dans un four qui peut atteindre les 20.000 degrés par ionisation des atomes et un dégagement important d’énergie. Ces gaz sont ensuite injectés dans un champ électrique qui créé un plasma, soit un arc électrique contrôlé, qui ressemble à une flamme. Des boitiers en céramique et des parties de bracelets sont au préalable installés dans le four et avec la chaleur et les gaz vont donner une couleur très particulière à la céramique, dans les tons gris et d’un éclat assez dingue.
Je vous passe les procédés de gravures au laser femtoseconde, servant à graver des inserts de lunette par exemple, grâce à un laser qui produit des impulsions ultra-courtes dont la durée est de l’ordre de quelques femtosecondes à quelques centaines de femtosecondes. Notre oeil et notre cerveau n’ont pas le temps de suivre, mais la danse du laser est presque poétique.
Ou encore une salle réservée au montage et au contrôle de bracelets en acier ou céramique, où, des préparatifs du bracelets, jusqu’à son assemblage final, plusieurs machines extrêmement précises et fort bien programmées effectuent toute la journée des taches très répétitives à coup de rivet, prise de mesure laser pour contrôler la taille de toutes les pièces, jusqu’au contrôle final par un être humain. Oui, il y a encore des hommes et des femmes autour de ces machines.
Voici une courte explication de la naissance d’un boitier en céramique, et de tous les composants attenants. J’aurais aussi pu vous parler de la création des glaces saphir qui s’obtiennent par procédé de Verneuil et l’écoulement de fines gouttes d’alumine en fusion qui forment une calotte de saphir qui recevra ensuite quelques traitements et découpages avant d’atterrir sur la montre. Mais cette partie a lieu dans un autre site de Comadur.
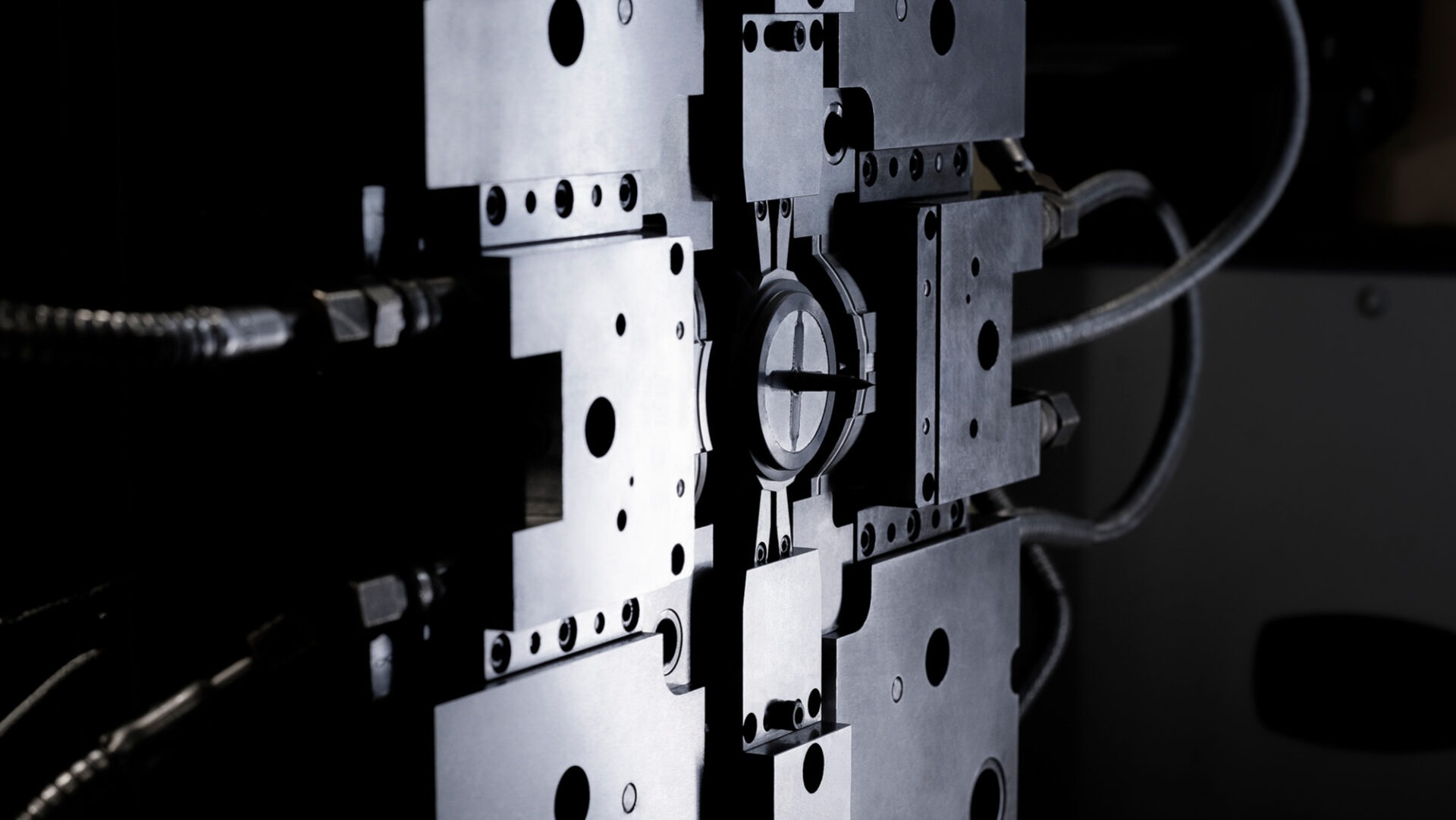
J’espère que vous pourrez pardonner mon excitation et ces mots plutôt nombreux. On se sent dans ces étages comme un enfant qui découvrirait l’univers robotique de toute une industrie, bercé par les odeurs de limaille, d’huile, dans un environnement plutôt chaud. Un Willie Wonka de l’horlogerie, en somme, et malgré tout ce que l’on peut penser sur ce genre de machinerie lourde, dévoile une certaine beauté, différente de celle dont nous avons l’habitude. Tout cela pour donner naissance à des petits garde-temps dont on se souviendra longtemps de la genèse. Rado assemble, certes, mais avec des designs assez uniques il faut l’avouer et surtout des procédés qui méritent notre attention.
Pour tout le reste, je vous laisse vous balader librement sur le site de Rado, où vous pourrez trouver d’autres explications et naviguer à travers tous ces univers.
Merci pour cette immersion poétique dans l’industrie de pointe de l’horlogerie moderne. Les savoir-faire traditionnels horlogers ne sont pas les seuls à nous émerveiller, l’industrie moderne en est également capable. Merci de nous le faire découvrir à travers ce bel article.